Hydraulic Block as a sample use case for AMable
This use case of LORTEK and HINE Co. shows how AMable services can support stakeholders in the uptake of additive manufacturing (AM). Hydraulic blocks can greatly benefit from AM through enhanced material usage and optimised flow conditions. Take a closer look at the steps!
Hydraulic Block

The challenge of the ADHYBLOCK idea was the redesign of a hydraulic block used in the wind sector taking advantage of benefits offered by additive manufacturing (AM).
The traditional block is manufactured using conventional technologies, that is, it starts from a solid metal block and internal channels are drilled and external interfaces are threaded. The machining of these conduits restricts their shape, being straight, with circular section and with 90° transition angles between channels. These transitions are critical points due to the disturbance of the fluid flow and are potential points for the formation of cracks and leaks in the block.
To solve these problems and additionally achieve other advantages such as weight reduction and better overall performance, the following specific challenges have been pursuit:
- To define an optimum design of the internal channels of the hydraulic block to obtain an efficient fluid flow avoiding any obstruction or turbulent flow.
- To design self-supporting channel geometries, that is, without inside supports, that are impossible to eliminate because they are inaccessible.
- To develop a design with a suitable strength to withstand the pressure of the fluid during the lifetime of the block and the loads during the manufacturing stage, i.e., threading of interfaces

The first step of the optimization has been the redesign of the transitions between conduits. For this, several transitions between channels have been rounded. The second step of the optimization has been the determination of the minimum wall thickness that supports the internal pressure of the fluid with a certain safety factor. After finite element modelling and fluid pressure simulations the minimum wall thickness for the maximum pressure (220 bar) was fixed at 2.5 mm, which is a significant reduction of the 4 mm distance between conduits used in traditional designs. Finally, the complete design was conceived by performing topology optimization to define the minimum material required between channels in order to withstand the loads during the CNC machining (threading) of the external interfaces.
Among the improvements provided by this solution are:
- Channels in the form of rounded elbows have been proposed, replacing conventional straight transitions. This modification will improve the flow of the fluid, consequently improving the functionality, performance and durability of the hydraulic block.
- The optimization of the design combining minimum wall thickness to bear internal fluid pressure and loads during machining, have given rise to a lightened block of 1.65 kg, which means a 73% weight reduction with respect to the weight of the original block.
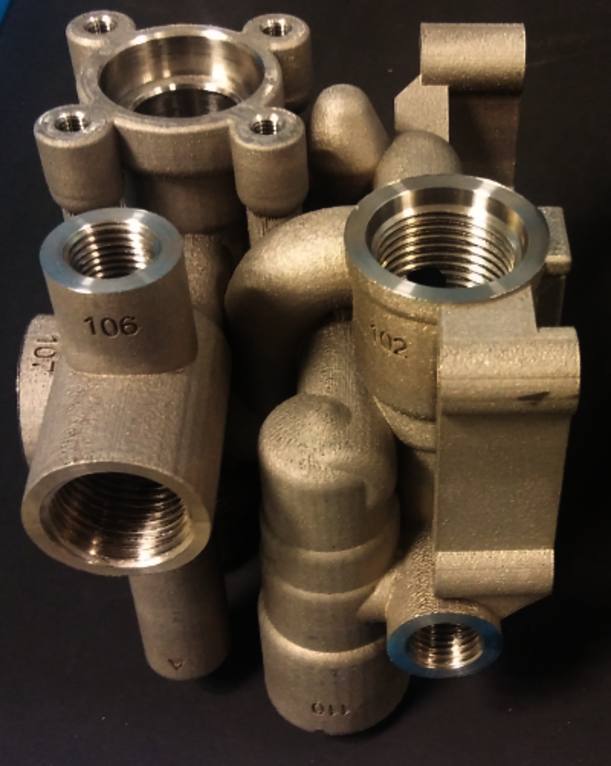
Improved functionality has been achieved by an optimum design of the internal channels, always looking for an efficient flow (laminar) of the fluid and avoiding any blockage or obstructions. The additive manufacturing and especially the Selective Laser Melting (SLM) technology, greatly facilitates this fact, since it opens multiple possibilities as far as design is concerned, making possible trajectories different from the straight lines and sections other than the circular ones currently used in conventionally manufactured hydraulic blocks.
Moreover, topology optimization has been implemented to define the minimum material required between channels in order to withstand loads applied during threading of external interfaces.
The main benefits with the new design and AM are:
- The optimization of the design gives rise to a lightened block. A reduction of 73% with respect to the weight of the original block was achieved.
- Fast iteration and design change implementation throughout the knowledge acquired in the project.
A consequent result of the simultaneous use of topological optimization and additive manufacturing technologies is the development of a new light-weight product that significantly reduces the amount of material necessary for manufacturing and reduces the costs associated with material.
Finally, the production process proposed for the development of the new hydraulic block product is more efficient, flexible and competitive. SMEs that use conventional technologies need the incorporation of innovative developments to maintain their competitiveness both in the national and international markets. For HINE, the advanced design of the hydraulic block with improved functionality will mean an important technological leap that can be applied to new generations of wind turbines.